Iron Castings
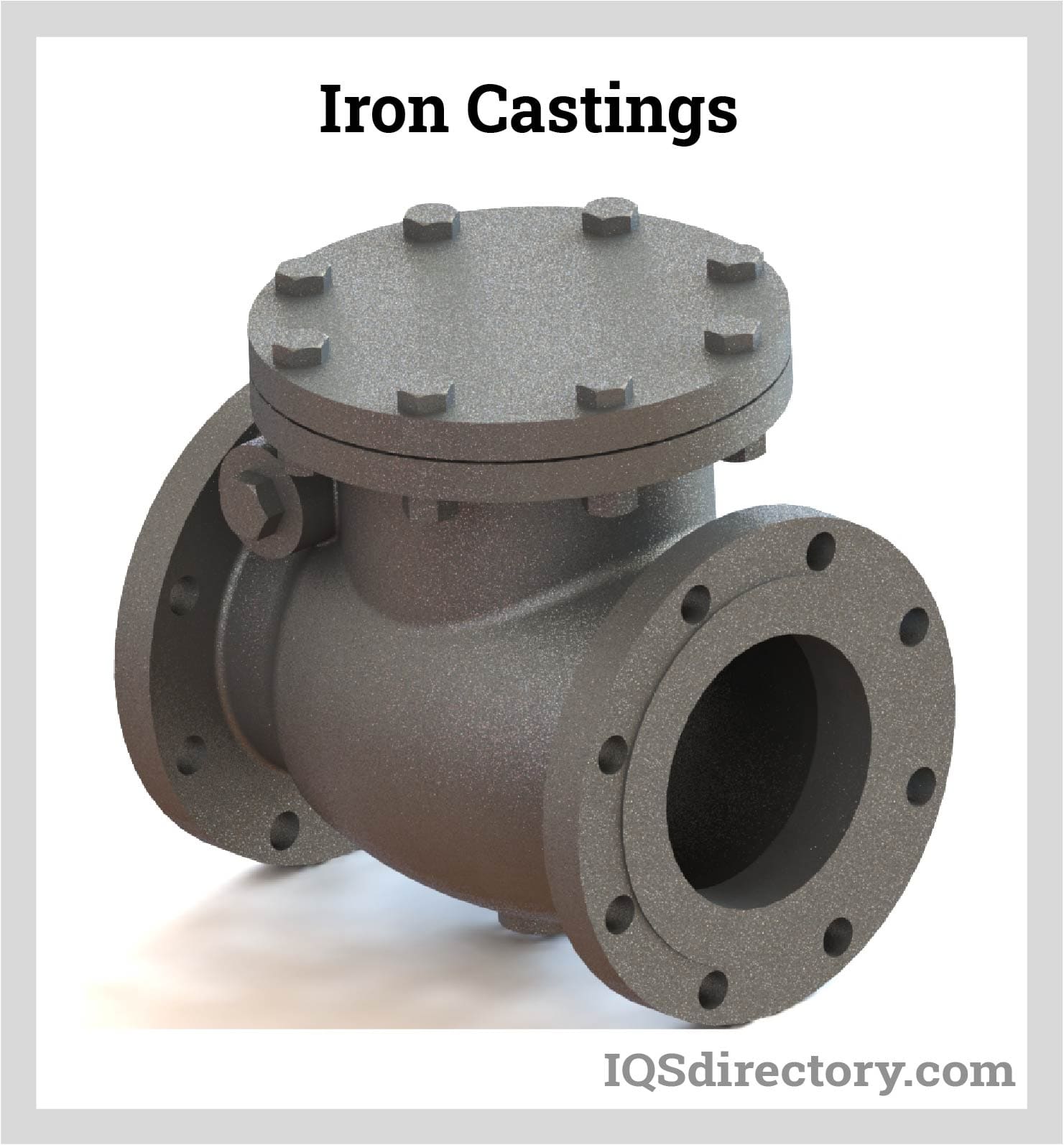
An iron casting is a hard product obtained from combining iron with carbon. This can be readily cast in a mold, and it contains a higher proportion of carbon compared to steel. The proportion typically ranges from 2 to 4.3...
Please fill out the following form to submit a Request for Quote to any of the following companies listed on
This article takes an in-depth look at investment casting.
You will learn more about topics such as:
Investment casting is a metalworking process that involves creating a ceramic shell over a wax pattern to produce parts with exceptionally smooth and uniform surfaces. The wax pattern is typically made using an aluminum die. After casting, the final products have minimal parting lines or mold marks, which are removed during secondary finishing to achieve the desired smoothness and uniformity.
Investment casting is a process that produces parts, components, and pieces with minimal waste and energy consumption. Its most notable feature is the high accuracy and exceptional tolerances of the finished products.
Investment casting, also known as lost wax casting or cire perdue in French, is an ancient metalworking method that dates back thousands of years. Originally developed in China, it was largely overlooked by modern industry until the 20th century, when advancements in technology made it easier to remove the wax from the casting.
During World War II, investment casting experienced significant growth due to its ability to produce exceptionally precise and flawless parts that traditional methods could not achieve. Following the war, it became the preferred process for industrial applications requiring complex and intricate designs.
Tooling for investment casting involves the wax injection dies used to create the wax patterns essential for the process. The specific tooling required depends on the part to be produced, as determined by the user. Tooling is integral to the design phase and includes Advanced Product Quality Planning (APQP), a design planning method developed in the 1980s.
At the core of Advanced Product Quality Planning (APQP) is a thorough examination of the production process and evaluation of each stage to prevent errors and avoid unnecessary repetitions. During APQP, every aspect of the end product is scrutinized, engineered, and discussed to ensure that the tooling comprising patterns and cores is precision-designed.
The die is the outcome of the APQP process. Wax injection dies are typically made from aluminum due to its excellent thermal properties, which allow it to dissipate heat quickly and reduce cycle times. Aluminum’s malleability and pliability make it easy to shape and form, and its resistance to wear from the wax injection process extends the die's lifespan.
Various types of waxes are used to create wax patterns, chosen based on factors like flow properties, reclamation ability, dimensional consistency, surface finish, and specific application requirements. Common waxes include filled pattern wax, non-filled pattern wax, runner wax, water-soluble wax, and sticky wax.
Filled pattern waxes contain additives that enhance the casting's strength, dimensional stability, and resistance to thermal expansion and shrinkage. These fillers include bisphenol, organic compounds, terephthalic acid, and cross-linked polystyrene.
Non-filled waxes do contain some fillers, though in smaller quantities compared to filled waxes. They offer excellent mechanical properties and thermal performance. These waxes are ideal for creating complex geometries and precise patterns and are significantly easier to dewax.
Runner waxes are designed for castings that need high mechanical strength but with a lower viscosity. They have a low melting point, which allows them to drain quickly from the ceramic mold.
Water-soluble wax is used for parts with complex internal patterns or designs involving intricate cores placed within the pattern. After the core is completed, the water-soluble wax pattern is positioned around it. As the pattern cools, the wax dissolves, leaving behind the desired internal structure.
After injecting the wax pattern around the soluble wax, the soluble wax is removed by immersing the assembly in a water bath with a small acid additive to accelerate the leaching process.
Sticky wax is used to bond pattern waxes together during assembly, providing a strong, long-lasting adhesion that helps prevent errors during frequent handling.
Wax is injected into the die or mold to form the pattern. The wax pattern is slightly oversized compared to the final part to compensate for the contraction that occurs in the ceramic mold. The die is then clamped shut, and an injection nozzle is aligned with the sprue, which is the channel through which the wax flows into the die cavity.
Wax pellets are melted in a holding tank that is connected to the injection press. This tank continuously agitates the mixture to maintain its uniformity. A hydraulic-powered cylinder then pushes the molten wax through a heated hose into the sprue, filling the die cavity.
Investment casting achieves high precision and produces finished parts in large quantities by assembling individual patterns onto a wax runner, to which the patterns are affixed. In addition to holding the patterns, the wax runner also functions as the metal feeding system, channeling molten metal to the individual parts during the casting process.
Wax runners are produced using the same method as the patterns. A metal element is placed at the end of the runner, around which the wax is injected. A pin attached to the metal element extends outward and will be connected to a hanger plate later in the process. Additionally, a ceramic cup is included as a funnel to guide the molten metal into the runner and patterns during casting.
The gates of the patterns are attached to the runner by melting the end of the gates on the surface, dipping them in a hot melt adhesive wax, such as sticky wax, and then pressing them onto the runner. As the melted wax cools, it bonds to the runner. A small torch is then used to weld and smooth the connection for a secure fit.
After assembling and setting the casting pattern, it is dipped into a slurry for coating. This slurry, composed of fine-grain silica, water, and a binding agent, forms a ceramic layer. The pattern is typically dipped multiple times to build up the coating to the desired thickness.
After the slurry dipping, the pattern assembly is coated with stucco according to the specifications outlined in the APQP. The stucco process begins with a thin layer and becomes progressively thicker with each subsequent application.
The shell coating is a crucial component of the process, as it must be strong enough to withstand all casting procedures. Multiple dips and layers of stucco are essential to ensure the shell's stability and durability throughout the casting process.
Different heating methods are employed to remove the wax from the hardened shell. A commonly used modern technique involves an autoclave, a steam heating device. The autoclave's temperature must be high enough to melt the wax, while the steam effectively removes any potentially volatile materials.
Investment casting molds are typically heated to 1800 °F (982 °C). Once the molds are thoroughly cleaned and reach the appropriate temperature, they are prepared for the injection of molten metal under pressure.
Casting involves injecting molten metal into the preheated mold cavities. The quality of the casting depends critically on the timing and temperature of this process. After pouring the molten metal, a vibrating machine gently shakes the ceramic shell for five to seven seconds to ensure even distribution. The metal, which has been melted from ingots, fills the shell and is then allowed to cool at room temperature.
After the shell has cooled and the metal has solidified, the shell material is removed using various methods. These methods include hammers, high-pressure water blasts, vibratory tables, chemicals, or specially-designed knockout machines. During the knockout process, the shell is tightly clamped to ensure uniformity, but removing the shell can be particularly challenging for parts with intricate or complex sections.
Cutting off involves separating the individual parts from the sprue or runner. Once the part is detached, the remaining gate stubs are ground away. Various methods can be used for this process, including chopping saws, torches, or lasers. In highly technical or high-production environments, a programmable cutting saw may be employed for precise and efficient removal.
Finishing processes vary based on the part’s design requirements and specifications. A common finishing step is grinding, which removes any remaining deformities or gate remnants. While the part's surface is typically quite smooth, additional polishing may be required to achieve a flawless finish.
Finishing can be achieved through various methods, including sandblasting, shot blasting, or other machining techniques.
Heat treatment aims to improve the mechanical properties and characteristics of the component. While the casting process can diminish a metal's strength, durability, and toughness, heat treatments help eliminate internal stresses. For investment casting, common heat treatments include vacuum solution annealing, hardening, tempering, and precipitation hardening.
Vacuum solution annealing aims to remove precipitates and transform the workpiece into a single-phase structure. Following this process, the workpiece becomes soft and ductile, making it suitable for subsequent hardening. At this stage, the workpiece is workable, machinable, weldable, and exhibits good dimensional stability.
Hardening involves heating the metal until it reaches its austenitic crystal phase, followed by rapid cooling. This process enhances the strength and wear resistance of the workpiece.
Tempering involves heating the workpiece to a temperature just below its critical range, maintaining that temperature, and then cooling it. This process reduces brittleness while carefully controlling the temperature to ensure that the hardness of the workpiece is not compromised.
Precipitation hardening, also known as age hardening, enhances the hardness of the workpiece. This process is carried out in a vacuum at temperatures ranging from 900 °F (482 °C) to 1150 °F (621 °C). It involves heating the workpiece, treating it with a solution, cooling it, and then reheating before a final rapid cooling stage.
Surface treatments for investment cast products encompass a range of techniques aimed at rust protection and enhancing corrosion resistance. The surface finish of an investment cast part can vary depending on the alloy grade and the product requirements. Common treatments include:
Although investment casting, also known as lost wax casting, has been utilized for thousands of years, advancements have improved the effectiveness of the process. These innovations focus on enhancing pattern development and the management of wax. A broader term for lost wax casting is evaporative pattern casting, referring to the removal or evaporation of the material used to create the pattern.
Although these alternative methods create patterns in different ways, they are similar to investment casting and can be viewed as offshoots or variations of the process. The primary differences among these methods lie in the materials used to create the patterns or the techniques employed in pattern formation.
Lost foam casting has become popular as an alternative to investment casting, particularly for its suitability in mass production and automated processes. This method, a recent addition to evaporation casting, was developed by H. F. Shroyer in 1958. It involves using polystyrene foam, which is placed in casting sand, to create the pattern.
In lost foam casting, an aluminum die is used to create the pattern, similar to investment casting. Polystyrene beads are placed in the mold or die and heated with steam. This heating causes the beads to melt and conform to the shape of the mold. As the beads expand, they take on the contours and dimensions of the die.
The individual patterns are attached to a sprue or runner and then sprayed with a refractory ceramic coating. The coated mold is placed in a vented container filled with sand to secure it in position. When molten metal is poured into the container, the polystyrene evaporates, creating space for the molten metal to fill the mold.
In some instances, patterns do not need to be shaped in a die and can instead be hand-carved. Polystyrene can be cut, shaped, and configured to the desired dimensions of the workpiece using machines or shaping tools. This method is often used for creating one-off parts or prototypes.
Lost foam casting is a manufacturing process used to produce intricate, decorative, and complex metal configurations, shapes, and designs. Engineers often utilize this method to create three-dimensional renderings of their conceptual designs.
Direct investment casting differs from traditional investment casting, known as indirect investment casting, in the method of pattern creation. In indirect casting, the pattern is first formed in a die to create a wax model. Multiple wax duplicates are then attached to a sprue or runner, coated with a ceramic solution, covered in stucco, and dewaxed. Finally, the mold is filled with molten metal to produce multiple versions of the component.
Direct casting differs in how the pattern is formed, using various techniques. One method involves carving the pattern by hand or machine to create a single version, which is then processed using the lost wax method. This approach is commonly used for producing prototypes, evaluating dimensions, or short production runs of finished parts.
Another technique involves using computer-assisted drafting (CAD) technology. With CAD, a three-dimensional model of the workpiece is designed and engineered. Similar to a CNC machine, the design is input into a stereolithography (STL) optical fabrication machine, which creates a three-dimensional representation of the pattern based on the provided data.
STL, or stereolithography, is a method for fabricating solid shapes using a photosensitive liquid polymer and a directed laser beam. This process involves building the object layer by layer, with each new layer added on top of the previous one to gradually form the three-dimensional geometric design. A diagram illustrating the STL process is shown below.
Water glass investment casting, commonly used in China, involves using water glass as the binding agent for the shell instead of ethyl silicate. This process, which originated in Russia in the 1950s, offers advantages in terms of material costs and production cycle efficiency.
The surface finishes achieved with water glass investment casting are comparable to those produced using silica sol casting technology, as it minimizes defects commonly associated with traditional shell methods. The process, operation, and parameters of water glass investment casting are less complex, allowing untrained or general workers to complete it, which enhances overall production and efficiency.
Investment casting is a highly versatile metalworking process used to shape a variety of components, including pipe fittings, automotive parts, marine hardware, and food machinery. It accommodates a broad range of metals, each offering distinct properties that enhance their suitability for different applications.
Investment casting can shape both ferrous and non-ferrous metals. Among ferrous metals, ductile iron, carbon and alloy steels, and certain grades of stainless steel are commonly used. For non-ferrous metals, copper alloys, magnesium, and aluminum are suitable, with aluminum being the most popular choice.
Aluminum alloys used in investment casting typically have a density of around 2.7 g/cm³ or slightly higher. These alloys are commonly used to produce parts for aircraft and engines. The most frequently used aluminum alloys in investment casting include A-356, A-357, C-355, and F-357, which contain elements such as silicon, magnesium, iron, and zinc. Components made from these alloys benefit from corrosion resistance, weldability, and, in some cases, exceptional strength.
Stainless steel is a ferrous metal alloyed with chromium to enhance its resistance to stains and corrosion. Various grades of stainless steel offer different beneficial properties, depending on their chemical composition. Due to its durability and resistance to high temperatures and corrosive environments, stainless steel is an ideal choice for components exposed to such conditions.
The primary grades of stainless steel used in investment casting are the 300 and 400 series. The austenitic 300 series stainless steel offers excellent corrosion resistance but does not achieve increased strength through heat treatment. In contrast, the martensitic 400 series stainless steel provides exceptional strength and machinability. It can be hardened through quenching and tempering, which enhances its strength further.
Carbon steel is a preferred choice for investment casting due to its ability to perform well under high-pressure conditions, as well as its wear resistance, exceptional strength, toughness, and hardenability. The properties of carbon steel are influenced by its carbon content, which enhances its hardness and strength during heat treatment.
Mid and low-carbon steels are commonly used in investment casting. Mid-carbon steel offers a balance of ductility, strength, and wear resistance and can be hardened and tempered through heat treatment. Low-carbon steel, while easily shapeable, does not gain strength from heat treatment but is valued for its ease of forming.
Nickel alloys are known for their high strength and resistance to heat, corrosion, and wear. They are weldable and fabricable and exhibit resistance to cracking and stress corrosion. Nickel alloy investment castings are primarily used in environments that involve high temperatures and corrosive elements.
Nickel alloy investment castings are favored for their tight tolerances and exceptionally smooth finishes, as well as their capability to be molded into complex and intricate shapes. Among the various metals used in investment casting, nickel alloys offer a cost-effective solution while maintaining high-quality performance.
Copper alloys are valued in investment casting for their corrosion resistance, thermal conductivity, and toughness. They are easy to cast and possess excellent machinability. Additionally, copper alloys offer impressive mechanical properties, along with strong resistance to friction and wear.
The copper alloys used in investment casting include series C-84500, C-85800, C-86000, C-87000, C-90000, and C-95000. This diverse range of alloys offers a broad selection to ensure the appropriate choice for various applications.
Cobalt alloys are known for their high strength, exceptional resistance to heat and wear, and natural resistance to oxidation. Their very high melting point makes them ideal for use in corrosive and chemically aggressive environments. Additionally, cobalt alloys exhibit creep resistance and resistance to thermal fatigue, making them suitable for high-temperature applications.
Cobalt alloys are composed of varying combinations of chromium, nickel, tungsten, and molybdenum, which affect their properties and types of resistance. For investment casting, commonly used cobalt alloys include grades 6, 21, 25, 31, and 93.
For many years, casting magnesium using investment casting was challenging due to the reaction between molten magnesium and the silica mold shell. Recently, the introduction of an inhibitor has addressed this issue, enabling the successful use of magnesium in investment casting.
Magnesium is prized for its lightweight nature and excellent strength-to-weight ratio. It is available in various alloys, such as AZ91D and AM60B, and other alloys like AZ81, AM50A, AM20, AE42, and AS41B are specifically chosen for their creep resistance and suitability for high-temperature applications.
Investment casting and centrifugal casting both produce exceptionally high-quality parts but differ in their processes and dies. Investment casting utilizes ceramic molds that are destroyed after the casting, while centrifugal casting employs permanent, reusable dies.
In addition to the differences in dies, there is a significant variation in the processes used to achieve well-formed, high-quality parts. Investment casting is a traditional method where molten metal is poured into a ceramic mold designed for single-use production.
In contrast, centrifugal casting involves a more dynamic approach where the mold is rapidly rotated as the molten metal is poured. The centrifugal force generated by the spinning mold ensures that the molten metal is evenly distributed against the interior surfaces of the mold or die.
Unlike investment casting, centrifugal casting is suited primarily for producing simple geometries with exceptional accuracy and high tolerances. Horizontal centrifugal casting is ideal for creating long parts like pipes, while vertical centrifugal casting is used for producing cylindrical shapes.
Centrifugal casting starts by pouring molten metal into a preheated spinning die, which can be oriented horizontally or vertically depending on the part configuration. The spinning die generates centrifugal force, which exerts pressure up to 100 times the force of gravity, ensuring the molten metal is evenly distributed over the interior surface of the die.
As the die spins, the denser portions of the molten metal are pushed against the walls of the die or its outer diameter (OD), while the less dense material and impurities accumulate towards the interior diameter (ID). This separation allows for the removal of impurities during the finishing process through machining.
An essential aspect of the centrifugal casting process is the equipment used, which must endure extreme heat and constant operation. Despite variations in equipment, all centrifugal casting systems share fundamental components, including a ladle, pouring basin, core, rollers, motor, and mold.
There are three main types of centrifugal casting: horizontal, vertical, and vacuum, each selected based on the part's requirements. In vertical centrifugal casting, the die rotates around a vertical axis. In horizontal centrifugal casting, the die rotates around a horizontal axis. Vacuum centrifugal casting involves pulling molten metal into the die under vacuum to minimize oxidation effects.
In vertical centrifugal casting, the equipment is oriented vertically, with the die spinning around its vertical axis. Molten metal is poured into the pouring basin located at the top of the apparatus. This method is ideal for producing cylinders where the diameter is greater than the height of the cast. It is commonly used for manufacturing components in the military, aerospace, and petrochemical industries.
In horizontal centrifugal casting, the die rotates around a horizontal axis. This method is well-suited for casting long tubular parts where the length exceeds the diameter. To counteract the effects of gravity on the molten metal, horizontal centrifugal casting requires exceptionally high rotational speeds. The mold features a closed and sealed cover at one end, with a pouring basin located at the opposite end.
Vacuum centrifugal casting was developed to address the challenges of casting metals that react with oxygen. In this process, a high-pressure vacuum pump is used to melt the metal, and a vacuum is employed to draw the molten metal into the centrifugal machine. Combining vacuum casting with centrifugal casting yields parts with directional solidification, eliminating porosity and reducing the need for finishing.
The vacuum centrifugal casting process minimizes oxidation, enabling better flow rates and precise temperature control. This results in parts that are uniform and possess tight tolerances.
A key benefit of centrifugal casting is its ability to produce components free of voids and shrinkage. During solidification, which occurs from the exterior shape of the mold inward, the process utilizes exothermic materials added to the interior diameter (ID) and a heat sink on the outer diameter (OD). This creates a temperature gradient that ensures directional solidification from the OD to the ID, enhancing the quality of the final component.
In centrifugal casting, the liquid metal from the interior diameter (ID) fills the casting, eliminating voids and defects. Despite the casting being solid, it still requires machining to address surface roughness and ensure concentricity.
The primary benefit of centrifugal casting is its increased yield, as the process eliminates the need for gates or risers, thereby reducing finishing time. The control over directional solidification ensures the production of uniform parts and components.
Centrifugal casting may be the ideal choice for the following reasons:
Investment casting is a widely favored method for producing a diverse range of parts and components. This process enables the creation of intricate and complex shapes from a broad selection of metals and alloys.
The simplicity of investment casting makes it ideal for high-production runs with exceptional dimensional accuracy. Originally adopted in the 20th century for the production of jet engine components in the 1940s where any inconsistencies or imperfections could not be tolerated investment casting has become a crucial method in modern manufacturing due to its ability to meet stringent quality standards.
The aerospace industry was the first to adopt investment casting for producing parts with exceptional tolerances and finishes. This method supports a wide range of metals suitable for flight components, ensuring precision and quality. Investment casting not only allows for the use of various metals but also produces high-precision parts with minimal material waste and limited energy consumption.
Aerospace components must endure extreme weather conditions, fluctuating pressures, and various forms of operational wear, demanding exceptional durability. Investment cast products provide the required consistency, precision, and tensile strength to meet and surpass these demands. Their primary advantage in aerospace applications is their precision, which ensures that interlinked parts align perfectly and integrate seamlessly.
Firearm manufacturers depend on investment casting for its ability to accommodate unique and intricate designs. Given the demands for precision and accuracy in firearm production, investment casting provides the necessary net shapes and can be executed with a range of alloys to meet specific requirements.
Investment casting reduces the amount of metal that needs to be removed during the finishing process. By utilizing CNC machining, manufacturers can produce uniform parts with minimal variation and at a lower cost.
The medical and dental fields require instruments and components with exceptional precision to meet stringent tolerances and dimensional standards. Investment casting is utilized to produce a variety of items, including surgical tools, implants, machines, stretchers, and wheelchairs.
The lifesaving potential of investment cast parts underscores the critical importance of their proper production. Each piece of equipment must be manufactured to the highest quality standards.
The primary requirement for locks is durability and resilience. Investment casting facilitates the production of both specialized and standard locks for various applications. The need for precise fitting means that casting must be accurate to the finest detail.
A diverse range of equipment is employed in food production, with many of its components relying on investment casting for manufacturing. Parts for the food industry are typically made from stainless steel or specialty alloys to ensure precision and durability. Investment casting is used to produce components for meat slicers, poultry processing equipment, ice machines, grills, and warming machines, among other food-related machinery.
Hydraulic and pneumatic equipment utilizes fluid power to transmit energy through gases or fluids. This sector requires various components, including ball valves, steam traps, impellers, needle valves, compressors, and pumps. Similar to the food and dairy industry, the hydraulics industry often employs stainless steel, aluminum, and specialty metals for these components to ensure durability and performance.
There are numerous methods available for producing metal parts, each offering distinct advantages in terms of production efficiency, quality, and precision. Among these methods, investment casting stands out due to its ability to produce precision parts with exceptional surface finishes. Its cost-effectiveness, design flexibility, and capacity for high-volume production make investment casting a preferred choice for modern manufacturing needs.
The numerous advantages of investment casting have established it as the premier metal fabricating process for both industrial and commercial products. Its precision, versatility, and efficiency make it the top choice for producing high-quality, complex parts across various applications.
Design freedom is crucial for creating complex and intricate parts with various internal and external shapes. Investment casting excels in this area, offering unparalleled flexibility as it is not constrained by size, thickness, or configuration limitations. This adaptability allows it to meet a wide range of manufacturing challenges, making it ideal for producing highly detailed and customized components.
Among the numerous advantages of investment casting, tighter tolerances are perhaps the most crucial. For parts that need to integrate seamlessly with other components, exact adherence to design specifications is essential. Investment casting achieves this by offering varying tolerances based on the part design. Symmetrical shapes with uniform walls can be produced with tighter tolerances compared to non-uniform or asymmetrical shapes, ensuring high precision and consistency in the final product.
Investment casting is renowned for producing superior surface finishes that require minimal post-production work. The process is distinguished by its ability to achieve a level of finish that surpasses other casting methods. This high-quality surface finish, coupled with the tight tolerances that investment casting can achieve, sets it apart from other manufacturing techniques. No other production method offers the same combination of precision and exceptional finishing quality, making investment casting the preferred choice for parts requiring both accuracy and a refined surface.
Production managers often highlight that defects are a major source of delays and increased labor costs. Defects in the manufacturing process lead to waste, additional machining, and slower production runs. Investment casting is highly valued for its ability to minimize defects, resulting in fewer adjustments and modifications. This low defect rate contributes to smoother production processes and reduced overall costs, making investment casting an attractive option for high-quality, efficient manufacturing.
Another significant cost in manufacturing is waste the material leftover after production. Investment casting excels in this area by requiring minimal post-production finishing, which greatly reduces the amount of waste generated. This reduction in waste offers several benefits, including lower production costs, reduced labor expenses, and quicker turnaround times. By optimizing material use and minimizing waste, investment casting contributes to both cost efficiency and environmental sustainability.
The reduction in waste also means there's no need for specialized equipment like deburring machines, heavy-duty grinders, or various cutting tools, which can be costly. This contributes to lower energy costs and increased efficiency, enhancing overall company performance. The streamlined process of investment casting ensures that resources are utilized effectively, further promoting economical and sustainable manufacturing practices.
Investment casting offers unmatched flexibility in production scale, capable of handling both small and large runs with precision. Whether the requirement is for a few parts or thousands, investment casting can efficiently produce components ranging from very small to those weighing hundreds of pounds. This adaptability ensures that investment casting remains a viable and effective solution for a wide variety of manufacturing needs, accommodating diverse production volumes and part sizes.
Investment casting's versatility extends to its ability to work with a vast array of metals and alloys, which is a significant advantage over other casting methods. Whether dealing with ferrous, non-ferrous, or specialty alloys, investment casting can accommodate nearly any type of molten metal, ensuring the production of reliable and high-quality parts. This broad material compatibility makes investment casting an ideal choice for manufacturing components across various industries, meeting diverse and demanding requirements.
Sustainability is a crucial factor in modern business practices, and investment casting aligns well with this principle. The process allows for the reuse of patterns, wax, and metal from runners, significantly reducing waste and lowering costs. By recycling these materials, investment casting not only contributes to environmental conservation but also enhances cost-efficiency, making it a popular choice for companies focused on sustainable production practices.
Investment casting's ability to produce components with minute, intricate details is unmatched by many other casting processes. This precision is why it was selected to support the aerospace industry and the development of the first jet-powered aircraft. As technological advancements continue to evolve, the demand for flawless parts and accurate dimensional tolerances will only grow, reinforcing investment casting's role in producing high-quality, detail-oriented components.
From the initial pattern creation to the formation of the ceramic shell and the final cut-off of parts, every step in the investment casting process is meticulously designed to ensure the production of intricate and precise details with exceptional accuracy.
Several factors influence the quality and accuracy of investment cast parts. Key considerations include the structure of the part, the casting material, the molding process, shell making, and the injection of molten metal. Any errors in these stages can affect the shrinkage rate, leading to deviations in the final dimensions and impacting the overall quality of the cast parts.
The first crucial step in the investment casting process is the creation of the wax pattern. This pattern must be produced with a high degree of precision and accuracy, as any imperfections or deviations at this stage can be transferred to the final cast part. The quality of the wax pattern directly impacts the overall success of the casting, influencing the final dimensions, surface finish, and functionality of the component.
The casting structure is significantly influenced by the thickness of the part's walls. If the walls are too thick, they can lead to increased rates of shrinkage, potentially causing defects such as voids or warping. Conversely, if the wall thickness is too thin, it may result in inadequate strength and potential issues with the structural integrity of the casting. Additionally, if the free systolic rate referring to the rate at which the molten metal flows into the mold is too large, it can impede proper shrinkage, leading to smaller-than-intended dimensions and other defects.
In casting processes, the material used plays a crucial role in determining the final quality of the part. Specifically, low carbon content in the material can reduce the rate of shrinkage during solidification. This is because materials with lower carbon levels typically have less propensity for volumetric contraction, which helps in achieving more stable and consistent dimensions in the final cast part.
The injection pressure and temperature are crucial factors in the casting process. Proper pressure ensures complete and uniform filling of the mold, while temperature affects the metal's flow and filling ability. Balancing these variables is essential for achieving accurate and defect-free cast parts.
The choice of material for making the shell can significantly impact the shrinkage rate. Materials like zircon sand, with a low expansion coefficient, are preferred as they help maintain dimensional accuracy throughout the casting process.
Improper heating of the shell can lead to decreased shell expansion, negatively affecting the dimensional accuracy and overall quality of the cast part.
The injection temperature is critical for casting quality. If it is too high, it can cause defects like coarse grains in the internal structure, while a low temperature may affect the fluidity of the molten metal. The optimal injection temperature depends on the specific alloy being used.
Maintaining a constant injection temperature is crucial to prevent shrinkage during the injection process. A higher, consistent temperature helps ensure the production of precise and accurate parts without requiring additional energy.
An iron casting is a hard product obtained from combining iron with carbon. This can be readily cast in a mold, and it contains a higher proportion of carbon compared to steel. The proportion typically ranges from 2 to 4.3...
Lost wax casting is a casting process that uses a wax pattern to create a ceramic mold for creating a part or product design. It has been known over the years as lost wax or precision casting due to its accuracy in recreating parts with precise tolerances...
The casting process is an ancient art that goes back several thousand years to the beginning of written history. The archeological record has finds that document the use of the casting process over 6000 years ago around 3000 BC or BCE...
Aluminum casting is a method for producing high tolerance and high quality parts by inserting molten aluminum into a precisely designed and precision engineered die, mold, or form. It is an efficient process for the production of complex, intricate, detailed parts that exactly match the specifications of the original design...
Aluminum forging is a method for processing aluminum alloys using pressure and heat to form high strength, durable products. The process of aluminum forging involves pressing, pounding, and...
Cold forging is a metal shaping & manufacturing process in which bar stock is inserted into a die and squeezed into a second closed die. The process, completed is at room temperature or below the...
Copper and brass forging is the deformation of copper and brass for the purpose of manufacturing complex and intricate shapes. The temperature at which copper and brass are forged is precision controlled and...
Die casting is a high pressure metal casting process that forces molten metal into a mold. It produces dimensionally accurate precision metal parts that have a flawless smooth finish...
Forging is a metal working process that manipulates, shapes, deforms, and compresses metal to achieve a desired form, configuration, or appearance outlined by a metal processing design or diagram...
Permanent molding casting is a casting process that uses strong durable reusable molds to produce parts and components using molten metals. The molds for permanent mold casting are made from steel or...
Rolled ring forging is a metal working process that involves punching a hole in a thick, solid, round metal piece to create a donut shape and then squeezing and pressuring the donut shape into a thin ring...
Sand casting is a manufacturing process in which liquid metal is poured into a sand mold, which contains a hollow cavity of the desired shape and then allowed to solidify. Casting is a manufacturing process in which...
Forging steel is a manufacturing process used to shape steel by using localized compressive forces, which include hammering, pressing, and rolling. It is a widely used method for producing high quality steel products...
Zinc die casting is a casting process where molten zinc is injected into a die cavity made of steel that has the shape, size, and dimensions of the part or component being produced. The finished cast zinc product has...